Einkaufslexikon
Materialbedarfsplanung: Definition und wichtige Aspekte für Einkäufer
Material Requirements Planning (MRP) unterstützt Unternehmen dabei, den richtigen Materialbedarf zur richtigen Zeit am richtigen Ort bereitzustellen und schafft damit die Basis für eine effiziente Produktion. Dieser strukturierte Überblick zeigt Ihnen, wie Sie MRP im Einkauf optimal einsetzen und dadurch Kosten senken sowie Lieferengpässe vermeiden können.
Material Requirements Planning auf den Punkt gebracht:
Material Requirements Planning (MRP) ist ein computergestütztes System zur Berechnung von Materialbedarfen und optimalen Bestellzeitpunkten basierend auf Stücklisten, Lagerbeständen und Produktionsplänen. Für den Einkauf ermöglicht es eine präzise, zeitgerechte Beschaffung und verhindert sowohl Materialengpässe als auch überhöhte Lagerbestände.
Beispiel: Ein Automobilzulieferer nutzt MRP, um für die Produktion von 1.000 Steuergeräten pro Woche den exakten Bedarf von 4.000 Mikrochips, 2.000 Platinen und 6.000 Gehäuseteilen zu ermitteln und diese unter Berücksichtigung der Lieferzeiten (6 Wochen für Mikrochips, 3 Wochen für Platinen) rechtzeitig zu beschaffen.
Einführung in das Material Requirements Planning
Die Materialbedarfsplanung (Material Requirements Planning, MRP) ist ein fundamentales Konzept im modernen Produktionsmanagement und der Logistik. Sie stellt einen systematischen Ansatz zur Planung und Steuerung von Materialflüssen in Produktionsunternehmen dar. Durch die präzise Berechnung von Materialbedarfen, Bestellmengen und Bestellzeitpunkten ermöglicht MRP eine effiziente Lagerhaltung und optimierte Produktionsabläufe. In einer Zeit, in der Ressourceneffizienz und Just-in-Time-Produktion immer wichtiger werden, gewinnt die Materialbedarfsplanung zunehmend an Bedeutung. Dieser Leitfaden gibt einen umfassenden Überblick über die Grundlagen, Methoden und praktischen Anwendungen der Materialbedarfsplanung im modernen Unternehmensumfeld.
Was ist Material Requirements Planning (MRP)?
Material Requirements Planning (MRP) ist ein systematisches Verfahren zur Planung und Steuerung von Materialbedarfen in Produktionsunternehmen. Es stellt sicher, dass die benötigten Materialien in der richtigen Menge und zum richtigen Zeitpunkt verfügbar sind, um einen reibungslosen Produktionsprozess zu gewährleisten. MRP berücksichtigt Produktionspläne, Stücklisten, Lagerbestände und Lieferzeiten, um Einkäufern eine präzise Bedarfsprognose zu ermöglichen.
Kernelemente der Materialbedarfsplanung
Bedeutung für den Einkauf
Im Einkauf spielt MRP eine entscheidende Rolle für eine effiziente Materialversorgung und Kostenoptimierung. Durch genaue Bedarfsplanung können Einkäufer Bestellungen besser bündeln, Mengenrabatte nutzen und Lagerbestände reduzieren. MRP hilft, Überbestände zu vermeiden und das Risiko von Materialengpässen zu minimieren, was direkt zur Steigerung der Produktivität und Wettbewerbsfähigkeit des Unternehmens beiträgt.
Material Requirements Planning: Von manueller Planung zu digitaler Bedarfsermittlung
Aufbauend auf den theoretischen Grundlagen des Material Requirements Planning (MRP) wird klar, wie essenziell präzise Materialwirtschaft für effiziente Produktionsprozesse ist. In der Praxis stehen Unternehmen vor der Herausforderung, Materialengpässe zu vermeiden und gleichzeitig Lagerbestände gering zu halten. Traditionelle Planungsmethoden reichen oft nicht aus, um diesen Anforderungen gerecht zu werden, weshalb ein Wandel hin zu modernen, digitalen Lösungen notwendig ist.
Alt: Manuelle Materialplanung
Traditioneller Ansatz: In der traditionellen, manuellen Materialplanung wurden Bedarfsermittlung häufig anhand von Erfahrungswerten und statischen Excel-Tabellen ermittelt. Produktionspläne wurden auf Basis historischer Daten erstellt, ohne die dynamischen Marktanforderungen ausreichend zu berücksichtigen. Dies führte zu Überbeständen oder Materialengpässen, da Aktualisierungen zeitaufwendig waren und oft hinter den realen Anforderungen zurückblieben. Die fehlende Integration zwischen Abteilungen erschwerte die Kommunikation und verursachte Ineffizienzen im gesamten Prozess.
Neu: Material Requirements Planning (MRP)
Material Requirements Planning: Die moderne Implementierung von MRP revolutioniert die Materialbedarfsplanung durch den Einsatz von Computersystemen, die Produktionssteuerung, Stücklisten und Lagerbestände in Echtzeit verarbeiten. MRP ermöglicht eine dynamische Anpassung an aktuelle Marktbedingungen und Kundenaufträge. Durch die automatisierte Bedarfsermittlung und Auftragsabwicklung werden Prozesse beschleunigt und Fehlerquoten reduziert. Unternehmen profitieren von geringeren Lagerbeständen, optimierten Lieferketten und einer erhöhten Reaktionsfähigkeit auf Nachfrageänderungen, was insgesamt zur Kostensenkung und Effizienzsteigerung führt.
Praxisbeispiel: Elektronikfertigung
Ein führender Hersteller von Elektronikkomponenten stand vor der Herausforderung, seine Lieferfähigkeit trotz kurzfristiger Auftragsschwankungen zu gewährleisten. Durch die Einführung eines MRP-Systems konnte das Unternehmen seinen Lagerbestand um 30% reduzieren und zugleich die Termintreue auf 98% steigern. Die automatisierte Bedarfsplanung ermöglichte eine schnellere Reaktion auf Kundenaufträge, verringerte die Durchlaufzeiten um 20% und führte zu jährlichen Kosteneinsparungen von über 2 Millionen Euro. Diese Verbesserungen stärkten die Marktposition und erhöhten die Kundenzufriedenheit signifikant.
Fazit zur Material Requirements Planning
Material Requirements Planning (MRP) ist ein unverzichtbares Werkzeug für moderne Produktionsunternehmen. Es ermöglicht eine präzise Materialbedarfsplanung, optimiert Lagerbestände und reduziert Beschaffungskosten. Trotz Herausforderungen wie Marktdynamik und Systemkomplexität bieten neue Technologien wie KI und Machine Learning vielversprechende Möglichkeiten zur Weiterentwicklung. Der Erfolg von MRP hängt maßgeblich von der Datenqualität, Systemintegration und einem effektiven Lieferantenmanagement ab.
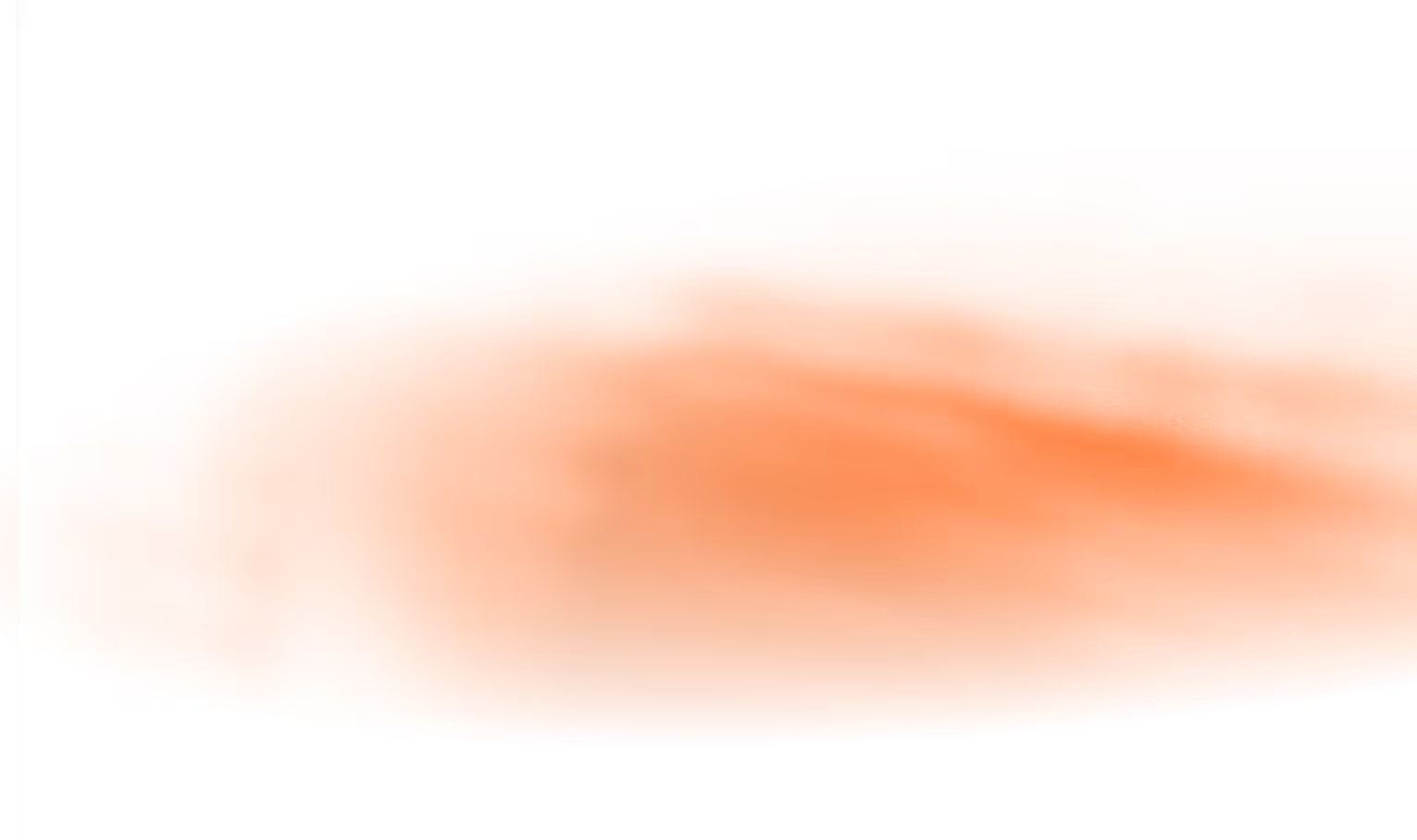